Producing smaller series and custom products adds complexity to the way operators work. Today, a range of digital tools are available to help them deal with their rapidly-changing and ever-widening range of tasks. Reach out to Sirris to explore the potential.
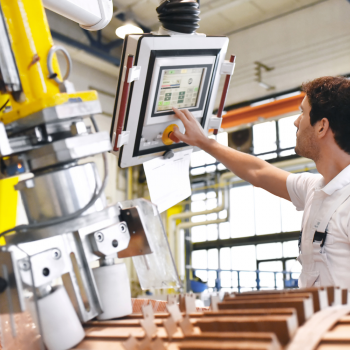
Digital operator support
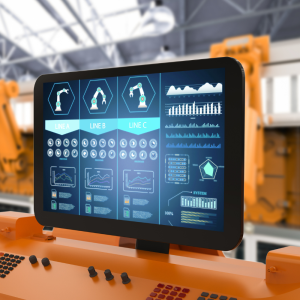
Providing the right information
Over 80% of technical production operators indicate that their work has become more complex in the past years. This is the result of a shift towards smaller batches, in which every product is somewhat different. The increased complexity often results in longer lead times and an uptake in quality control issues. The main reason for these issues is missing information. Fortunately, digital tools can be used to provide the right information, at the right time, to the right person. Depending on the study, significant improvements in both production lead time (up to 25%) and quality control (up to 100%) can be achieved. Let our experts guide the way!
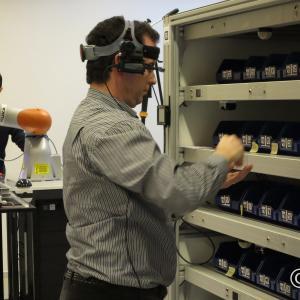
Broad range of applications
Digital tools can be applied in a wide array of situations. Digital work instructions are typically used for tasks where errors or forgetfulness are difficult to exclude, such as complex assembly operations or jobs with critical operation sequences. Augmented and virtual reality (AR/VR) applications are most frequently used for operator training. Here, the focus lies on improving both the speed and the quality of the training. A third typical area of application is remote support for operators (sales and maintenance), through the use of wearables like smart glasses. Are you interested in evaluating what application would best suit you? At Sirris we have all the expertise to help you on your way.
Digital work instructions: 5 reasons why
Up-to-date information
Operators always have access to the latest information - changes to instructions can be made at the last minute without disrupting production.
Personalised information
By scanning, for example, both the order and the operator, personalised instructions can be provided that take the level of the operator into account.
Diversified and interactive information
Information can be provided in different forms, including photos, animations and videos. Operators can work through checklists and benefit from two-way interactions that allow them to provide feedback to the information system as well.
Linked information
Because there is a direct link with the ERP/MES system, operators can log critical information, such as whether or not to perform an important quality control, or to record times (measuring production times).
Mobile information
The information can be provided via various carriers, such as smart glasses, tablets, screens or AR/VR headsets, which allow you to work when mobile - and even remotely.
Inspiring articles
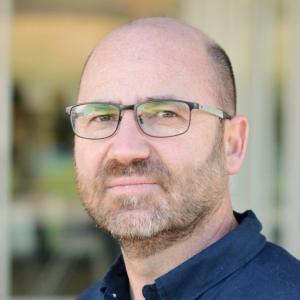
Immerse yourself in the world of mobile robot applications.
Our expert Christophe Michiels will gladly show you the ropes.